Marine engineering is constantly evolving. Van Oord has made a substantial contribution to the development of knowledge, technology and equipment in this field. Here, we highlight three innovations to which our ingenious people have contributed.
In the spotlight
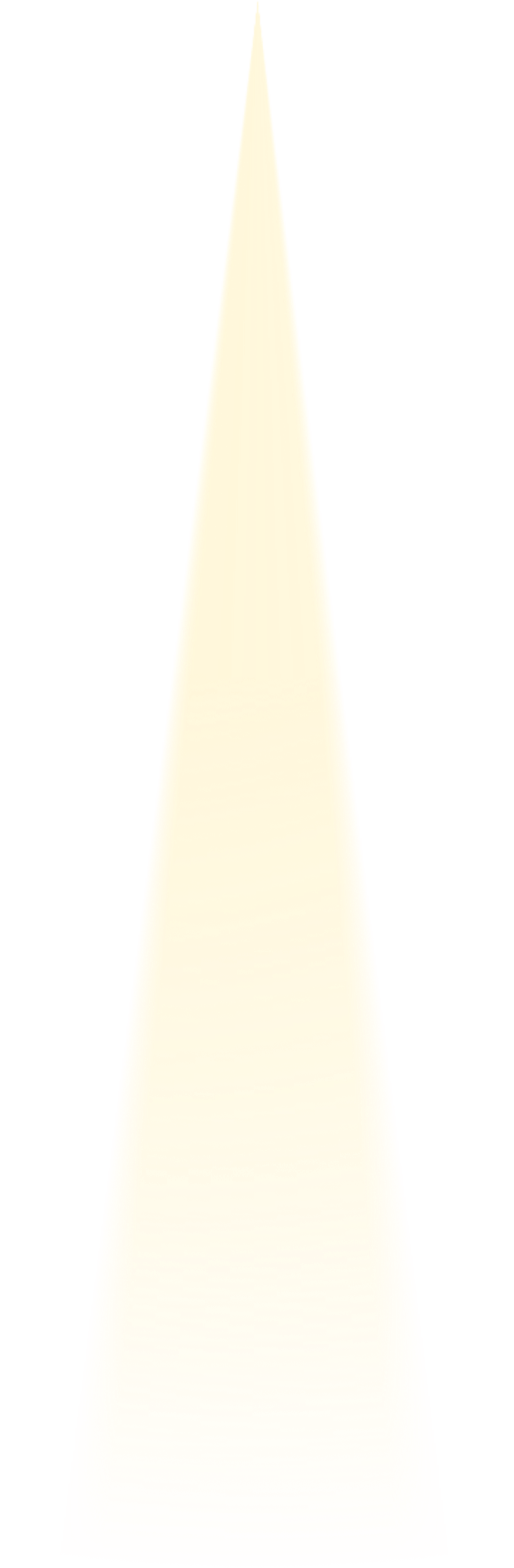
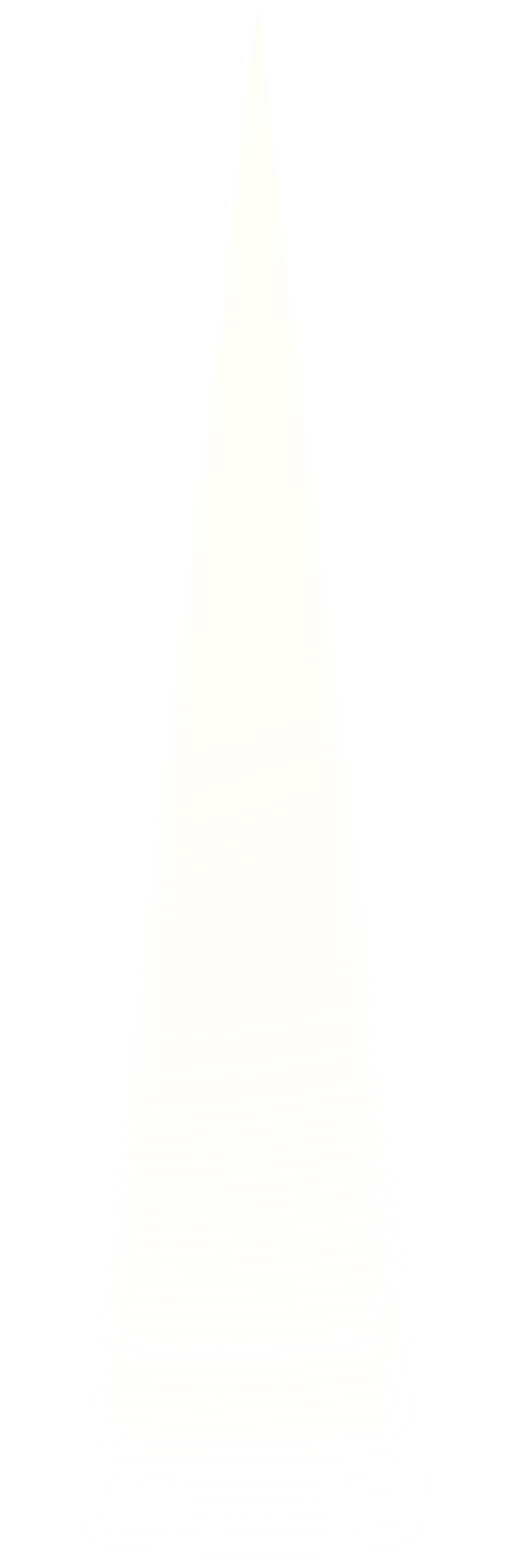
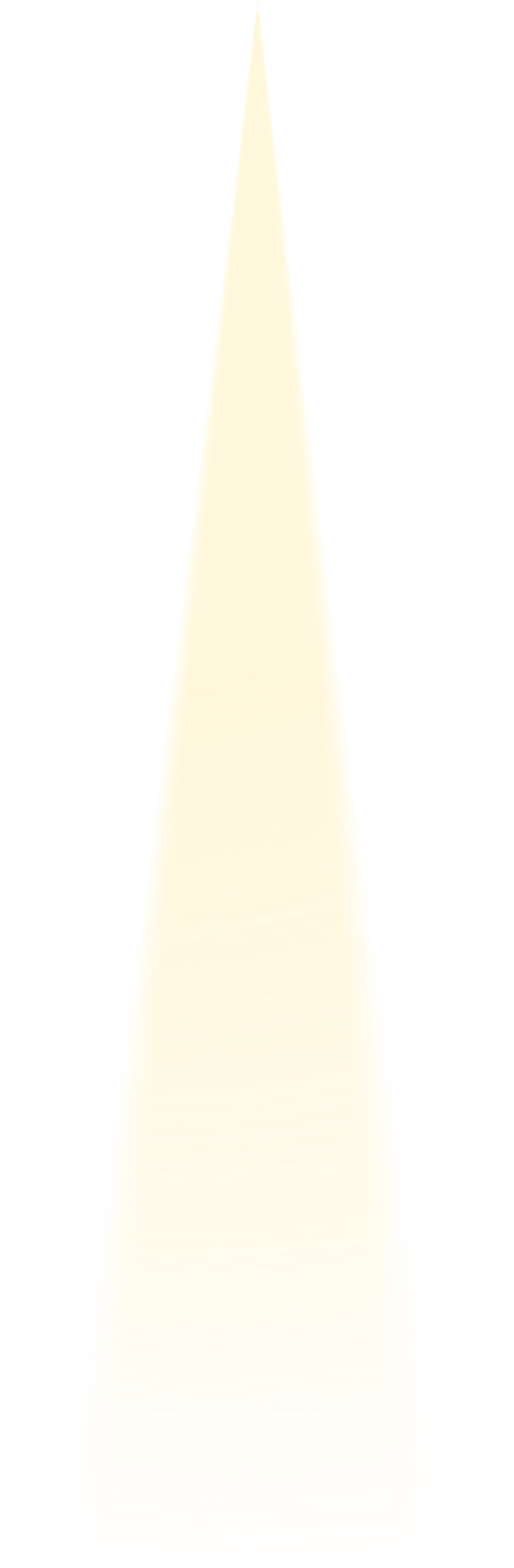
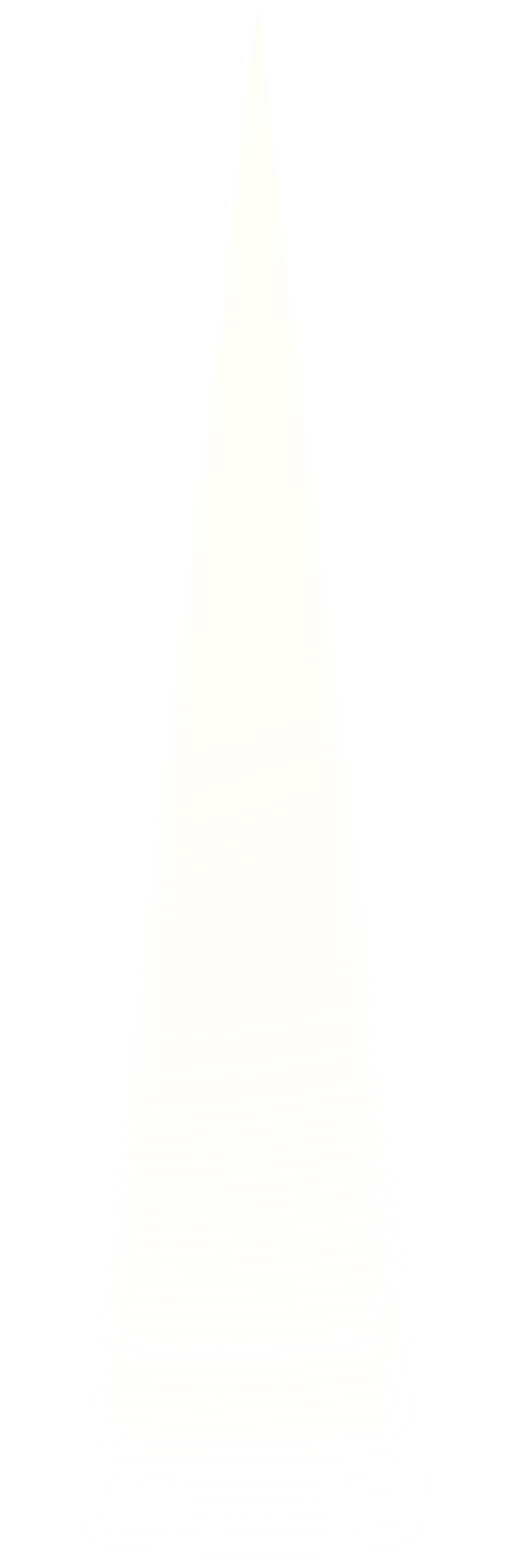
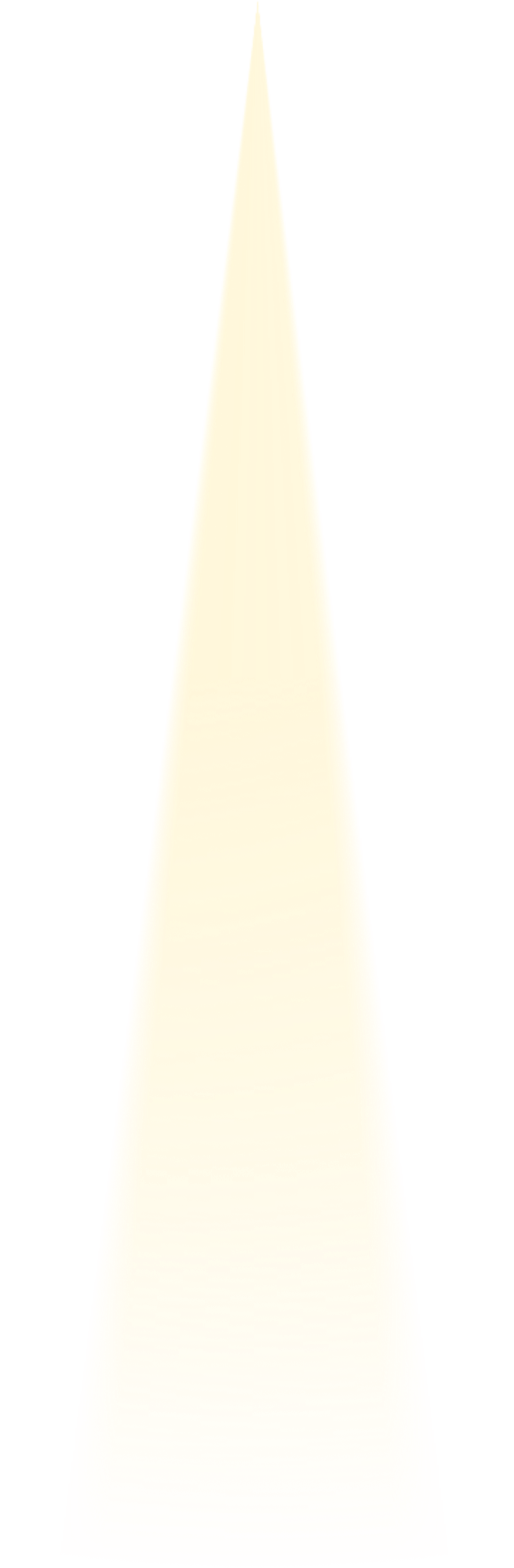
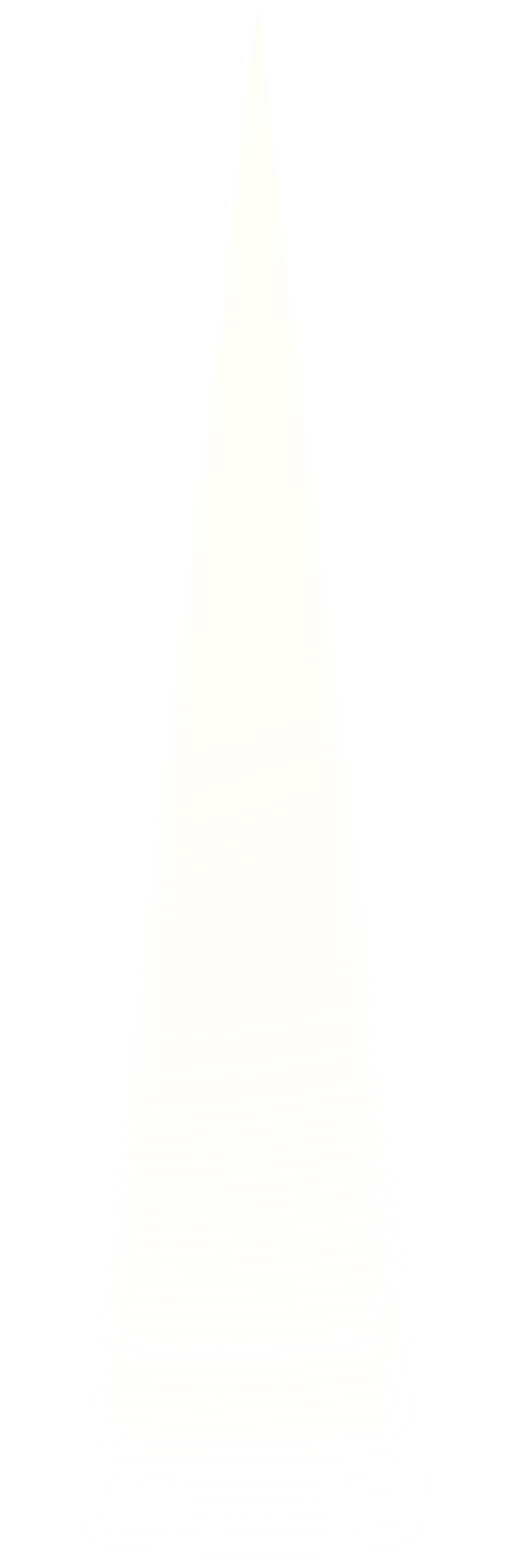
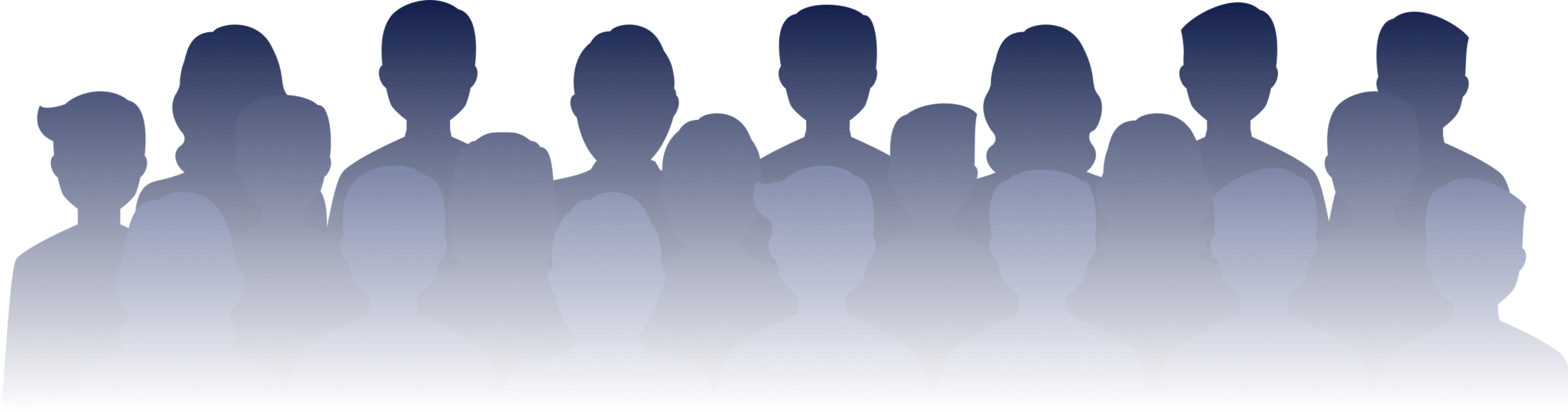
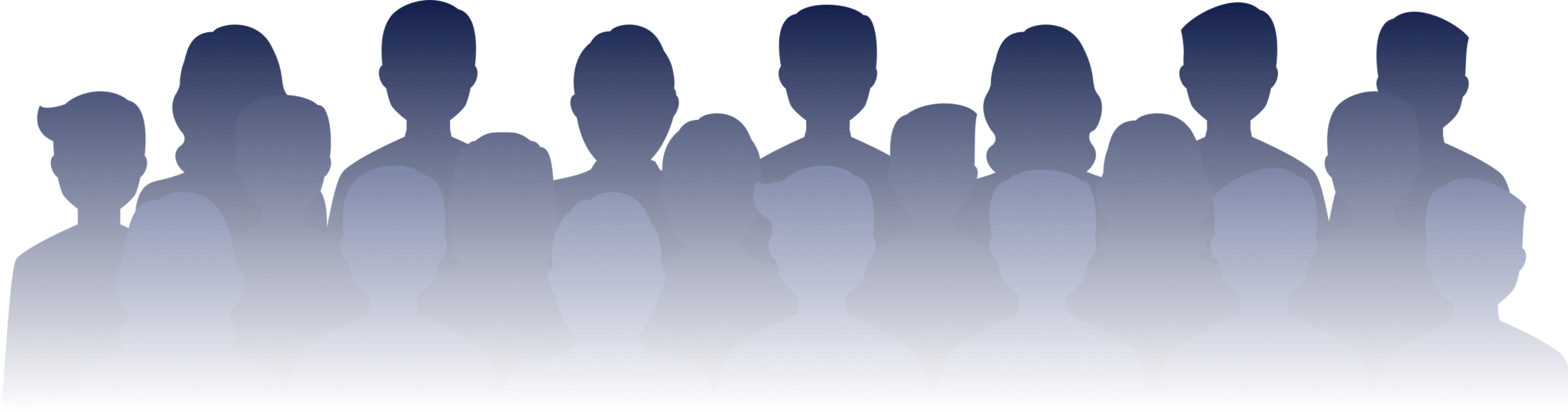
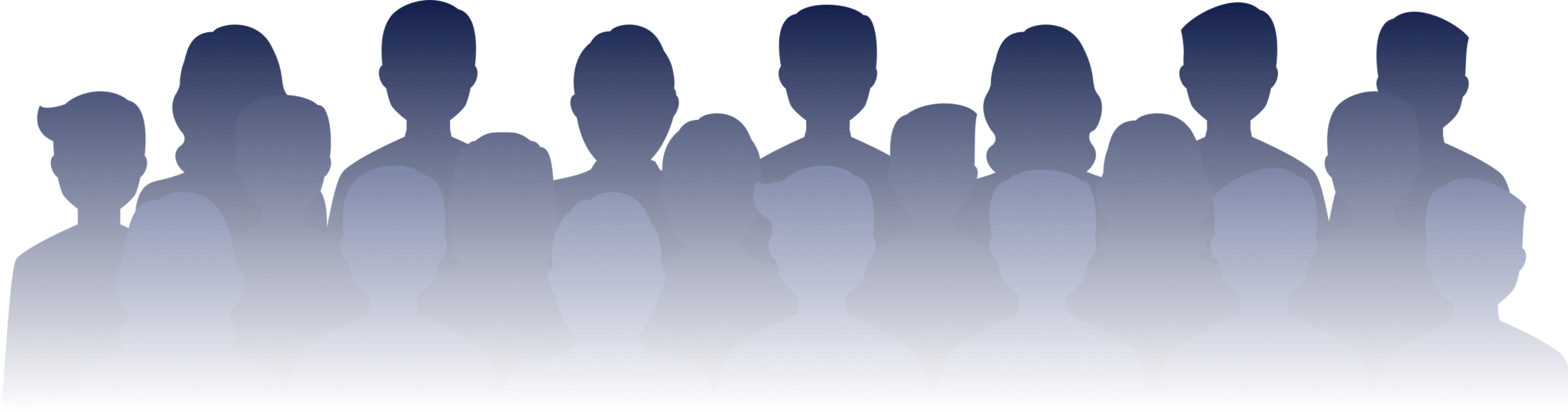
Back to start
Sjon Kranendonk
Manager Production Estimating
The rainbow method requires a lot of power. In our search for energy efficiency on board and to reduce our carbon footprint, Van Oord designed the latest vessels, such as the Vox Amalia and the Vox Alexia, with a double nozzle. This will require less pump power and will shorten the discharge time. We continue to search for ways of optimising our vessel output and improving the discharge methods.

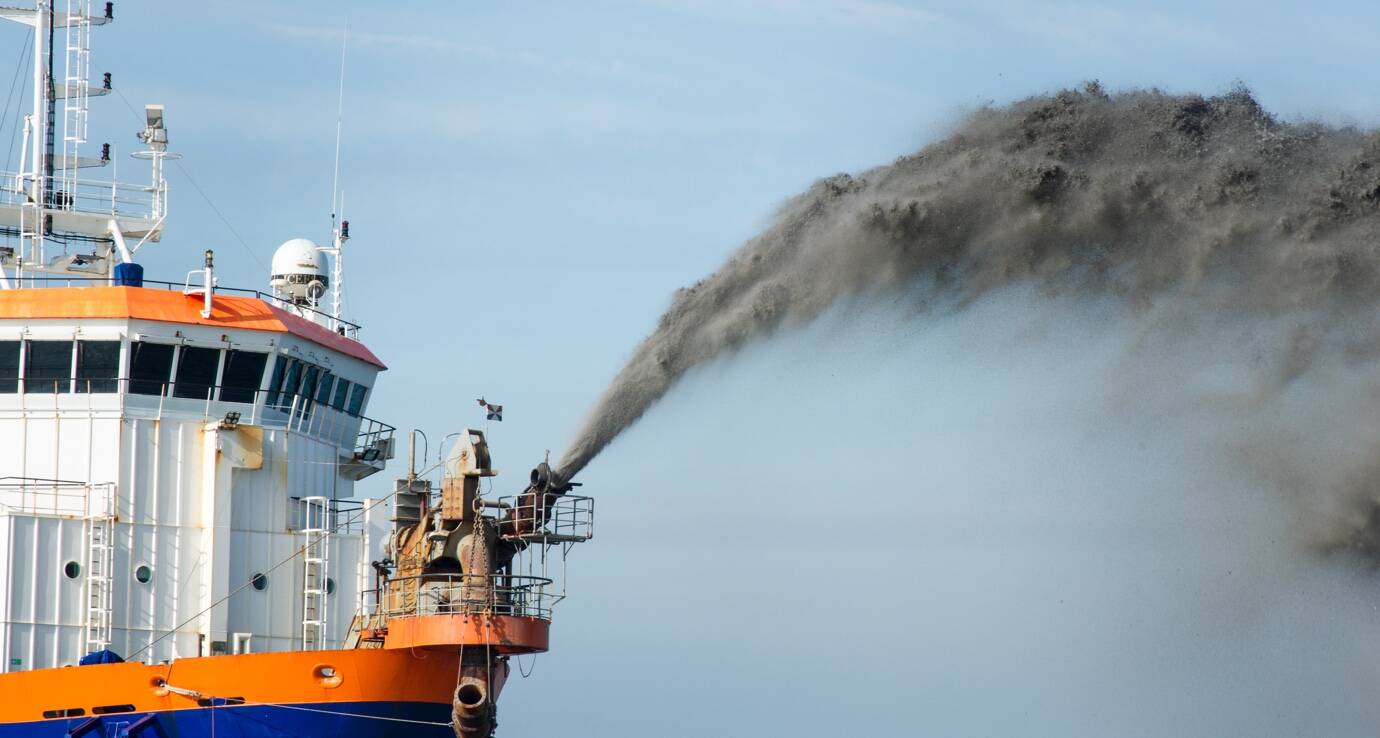
The rainbow technique was also ideal for beach and foreshore replenishment, although some adjustments were required because vessels sometimes need to work in areas with strong currents. To deal with such situations, the nozzle was shifted from the bow to the side of the vessel. This allows the vessel to direct their bow in the current and steady its position.
As the technique improved, knowledge about the correct mixture of sand and water grew, and the vessel pumps increased in power, the rainbow technique evolved to where it is today: a precise method that can be used to fill land reclamation sites, create islands in the middle of the ocean, and deposit sand at exact locations for beach replenishment projects or foreshore reclamation.
How it started
Before, vessels had to be situated in water deep enough to open their bottom doors; alternatively, sinker lines and pipelines had to be installed and auxiliary equipment deployed to pump the material to shore. Ingenious professionals thought up a method to lower these reclamation costs and expand their field of operation. The new method, introduced in the 1980s, was the rainbow technique. A nozzle installed on board of a trailing suction hopper dredger made it possible to discharge the material directly over the bow of the vessel.
Pinpoint accuracy
Besides lowering costs, the rainbow technique had other advantages. Land could be reclaimed quicker without having to move pipelines on shore. It also proved to be an effective method for creating steeper slopes.
Dubai’s landmark Palm Jumeirah or the archipelago The World could probably only be constructed economically using the rainbow method, introduced for the first time in the 1980s. Before then, trailing suction hopper dredgers discharged their load either by depositing it through their bottom doors or pumping it to shore through a pipeline.
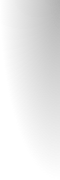
Reclaiming land quicker and at lower costs
Rainbow method
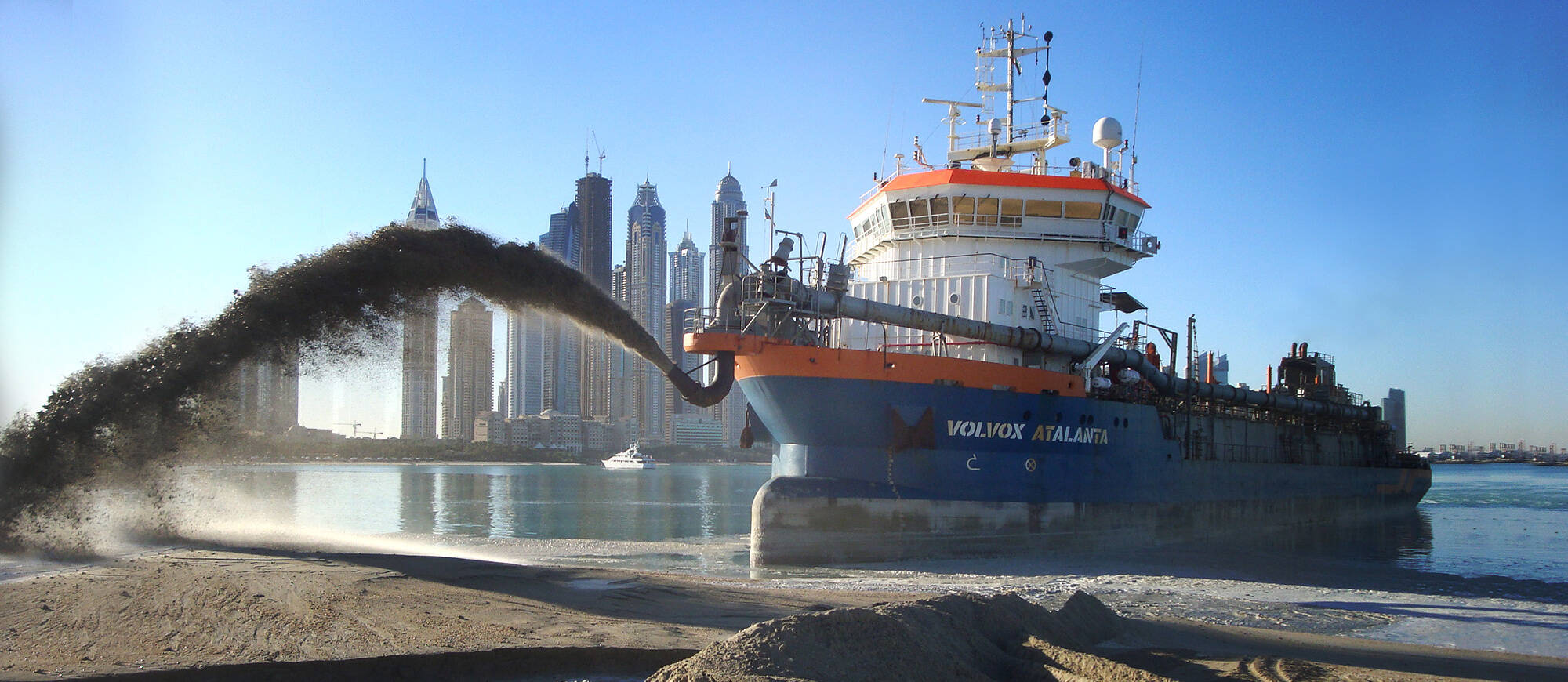
Back to start
Koos van Oord
Area Manager for Van Oord Offshore
The addition of the Bravenes to our fleet allows us to maintain our leading position in the market. Compared with other subsea rock installation vessels, the Bravenes can install rock very close to offshore platforms such as monopiles in offshore wind parks.

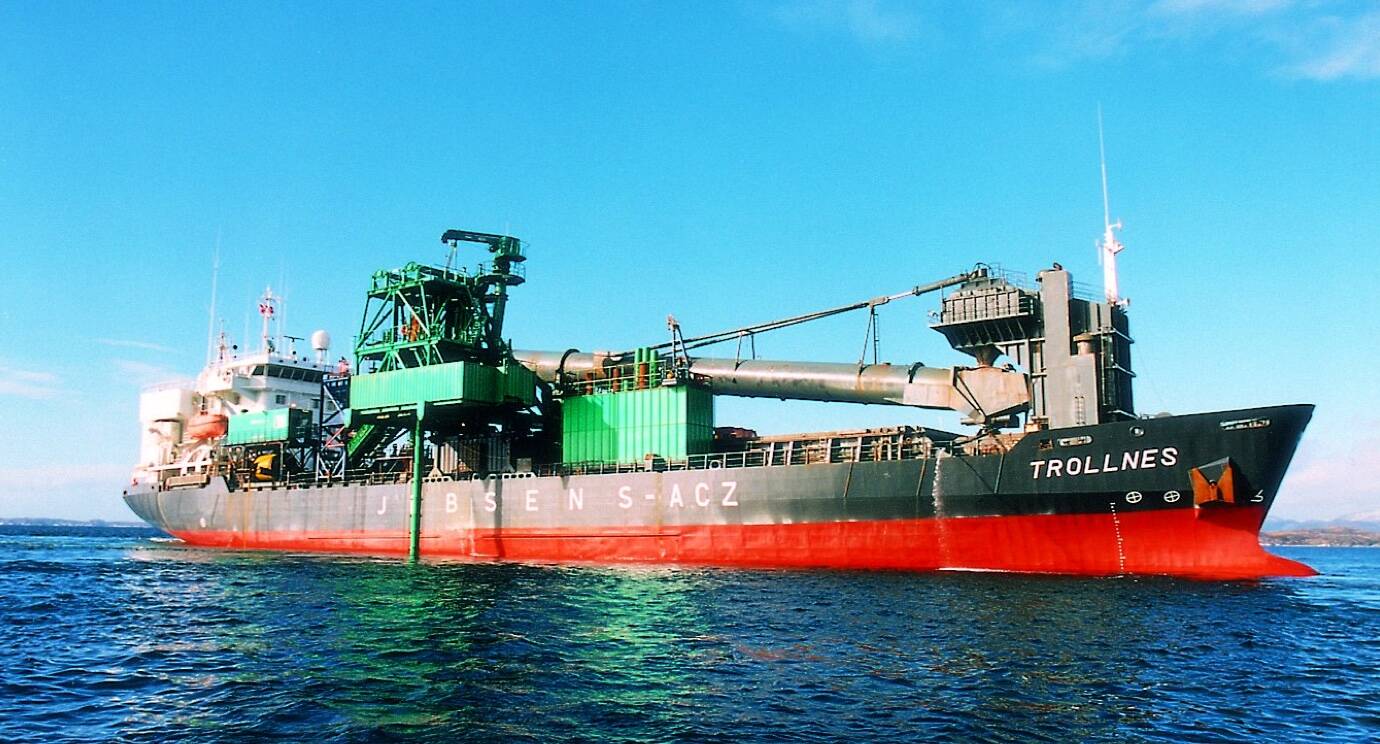
Brave new world
Offshore wind is a growing market for subsea rock installation. Generally, offshore wind parks are located in relatively shallow waters, where waves and currents have a bigger influence on the seabed than in deeper water. That means that larger rocks are needed to guarantee stable protection of foundations placed on the seabed.
The Bravenes has been designed to load both larger and smaller rocks and has the unique ability to install rock in different ways. Equipped with the latest innovations to improve vessel safety and efficiency, such as a fully automatic fallpipe loading and transport system, it raises the bar for the industry.
How it started
In the 1950s, we developed the side stone dumping vessel, replacing the manual installation method that had been used for centuries. These vessels were used successfully in shallow waters. It was the first step in improving safety, accuracy and efficiency.
Oil and gas exploration explored deeper waters and new rock installation techniques had to be developed. Once again, Van Oord rose to the challenge and developed its unique flexible fallpipe concept. The first flexible fallpipe vessel ever, the Trollnes, began operating under the Van Oord flag in 1991. Dynamic positioning and a remote-operated-vehicle ensures very accurate placement of rock in deep water. The flexibility of the fallpipe means it can operate in high waves and strong currents. Further investments of the system led to the capability to protecting a pipeline at a record-breaking depth of 1,277 metres by the Stornes, starting a new area of subsea rock installation.
Subsea Rock Installation (SRI) has been a core element of our business throughout the 150 years of our existence. After the Second World War, Van Oord was already the market leader in this field. At that time, rock was installed by hand. Thanks to a string of in-house and external innovations, manual labour has been replaced by a fully automated system.
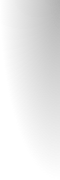
Improving safety and efficiency
Subsea Rock Installation
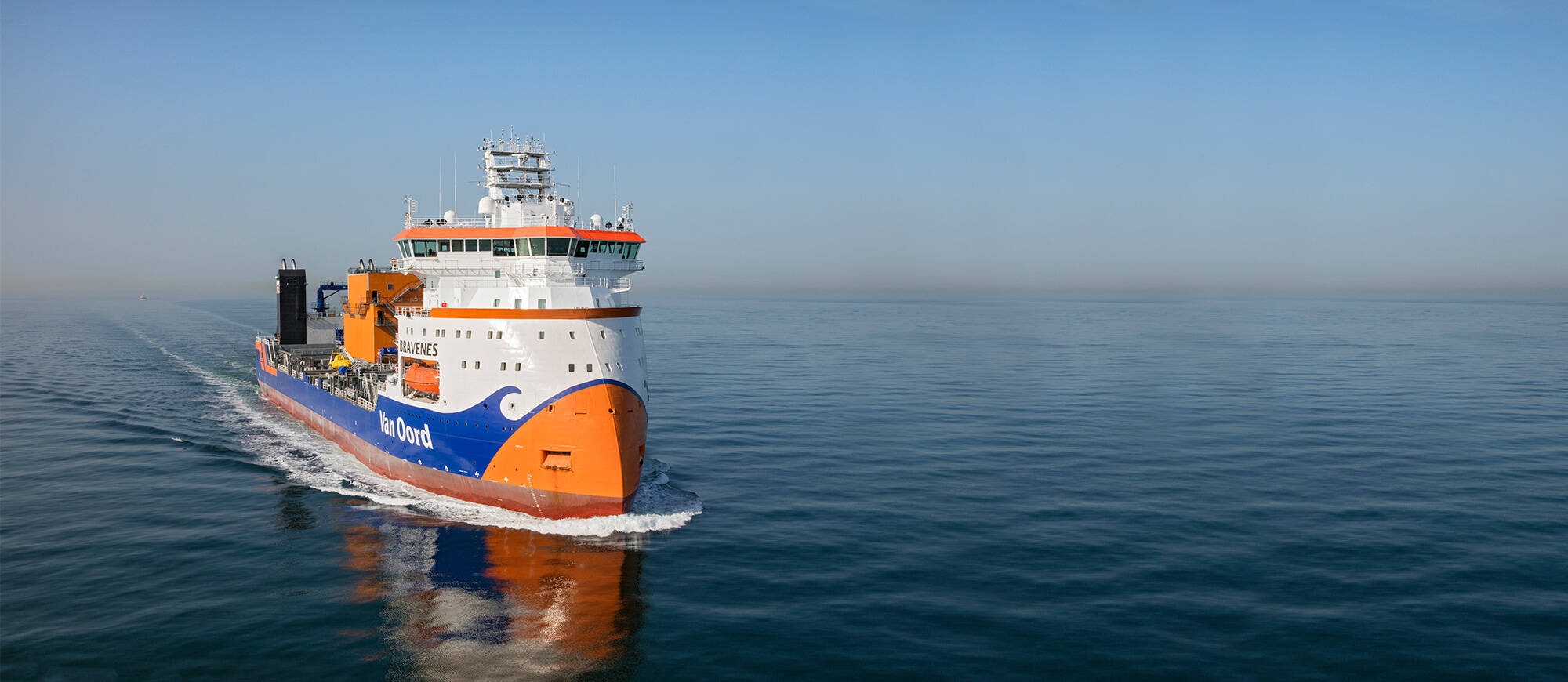
Back to start
Marcel Krijnen
Deputy Director of the Willem
Barentsz Maritime Institute
As a maritime institute we want to meet the demand for highly qualified personnel in the maritime sector. With the use of our simulators, we can reach that goal. On-the-job experience is always best, but the simulators these days are a really close second and invaluable in our curriculum.

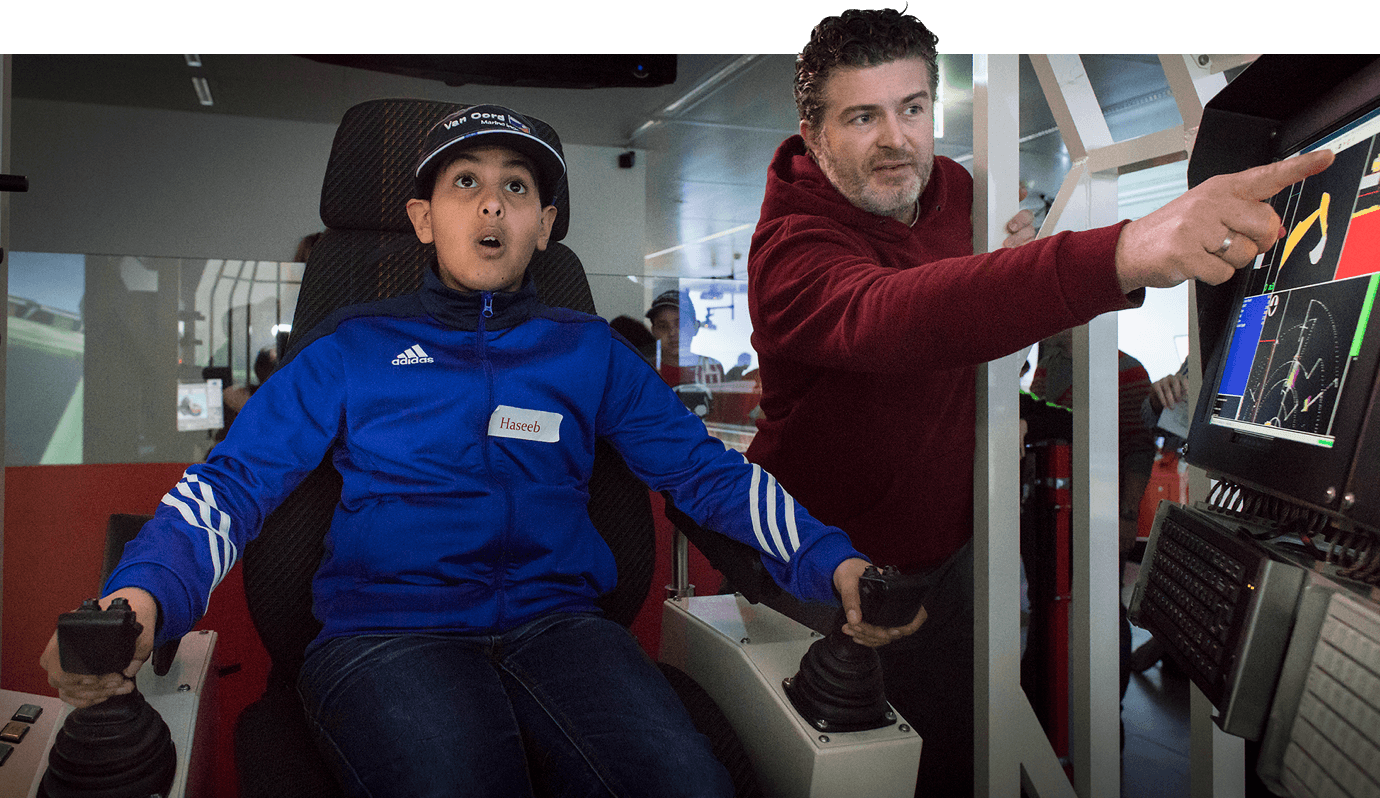
Ready for all conditions
The simulators have evolved over the years and we currently have three of them in-house giving a realistic view of project situations for three types of equipment. What makes our training programme stand out is that we emphasise on dredging production and automation and that our simulators can simulate any circumstance, from soil type to weather conditions.
We continue to improve and develop our simulators and training programmes and have partnered with the Willem Barentsz Maritime Institute to share best practices. That way, we’ll both be ready to train the dredging professionals of the future.
How it started
In the 1970s, dredging professionals wanted to gain more insight into the interaction between equipment and soil. That was the starting point of using simulators to obtain more knowledge. Van Oord played a major role in the implementation of these unique simulators and values their use up to this day.
The world’s first cutter suction dredger simulator came to life in the 1980s and one of Van Oord’s predecessors was involved in developing it. It was also the first time dredging schools started to use this technique to teach new dredging professionals the skills of the trade. The first trailing suction hopper dredger simulator was introduced in 1990s. Both types of simulators changed the manner of training forever.
At Van Oord we know the importance of keeping our professionals’ knowledge and skills up-to-date, and we’re always looking for ways to improve training facilities. The high-tech simulator training center at our Rotterdam head office is the perfect example.
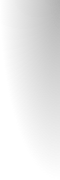
Changing the way we learn
Simulator
Training Center
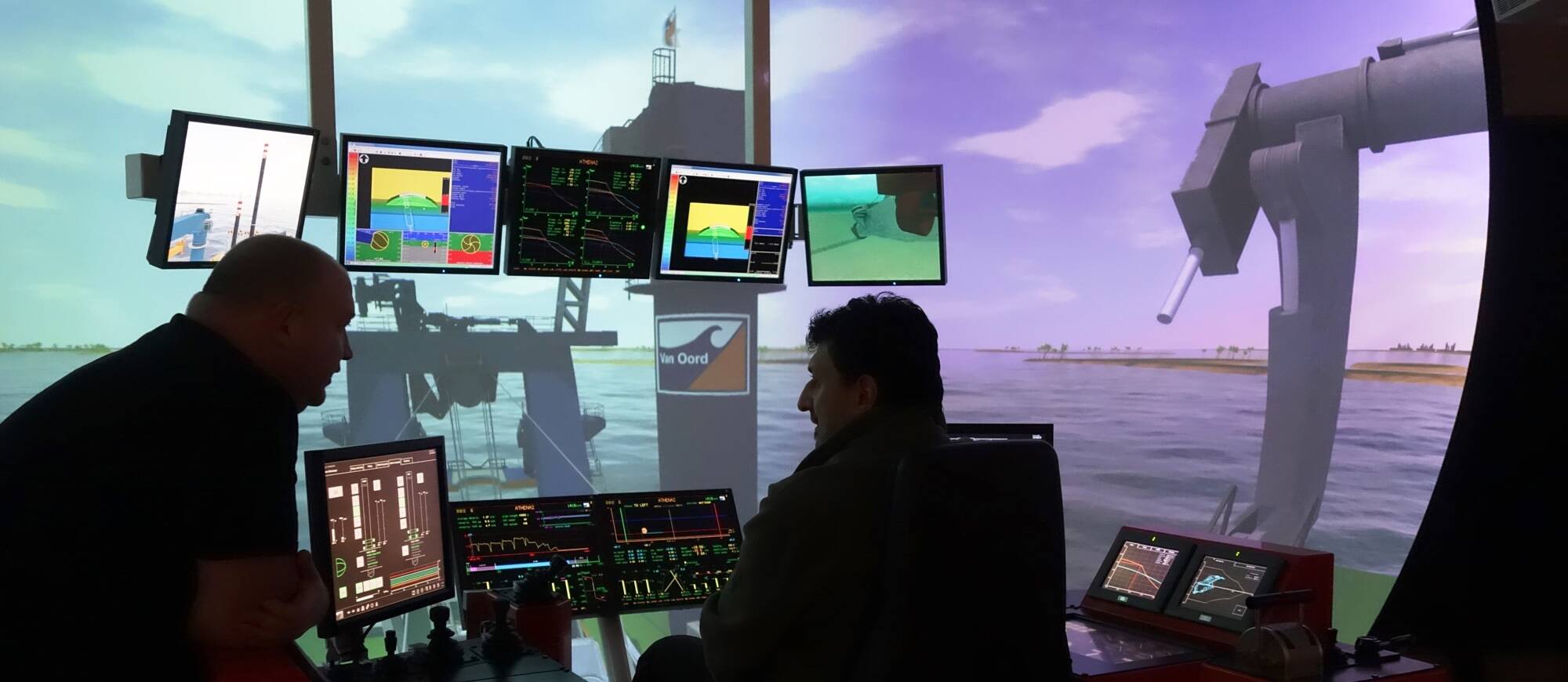
Changing the way
we learn
Simulator Training Center
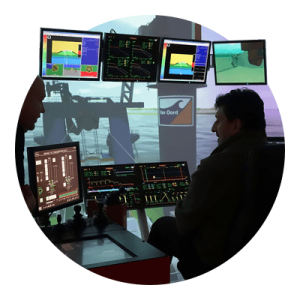
Improving safety and
efficiency
Subsea Rock Installation
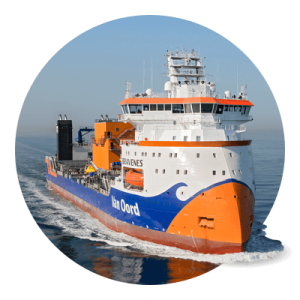
Reclaiming land quicker
and at lower costs
Rainbow method
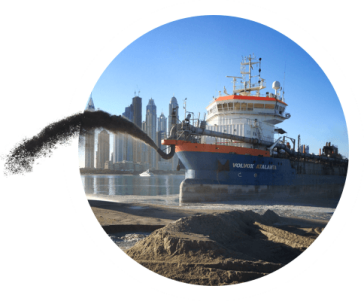
Marine engineering is constantly evolving. Van Oord has made a substantial contribution to the development of knowledge, technology and equipment in this field. Here, we highlight three innovations to which our ingenious people have contributed.
In the spotlight
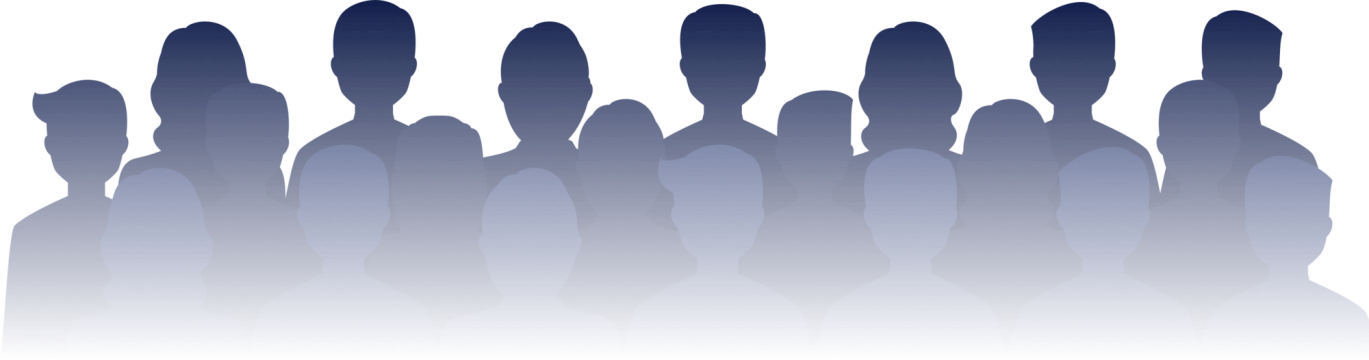
Sjon Kranendonk
Manager Production Estimating
The rainbow method requires a lot of power. In our search for energy efficiency on board and to reduce our carbon footprint, Van Oord designed the latest vessels, such as the Vox Amalia and the Vox Alexia, with a double nozzle. This will require less pump power and will shorten the discharge time. We continue to search for ways of optimising our vessel output and improving the discharge methods.
How it started
Before, vessels had to be situated in water deep enough to open their bottom doors; alternatively, sinker lines and pipelines had to be installed and auxiliary equipment deployed to pump the material to shore. Ingenious professionals thought up a method to lower these reclamation costs and expand their field of operation. The new method, introduced in the 1980s, was the rainbow technique. A nozzle installed on board of a trailing suction hopper dredger made it possible to discharge the material directly over the bow of the vessel.
Pinpoint accuracy
Besides lowering costs, the rainbow technique had other advantages. Land could be reclaimed quicker without having to move pipelines on shore. It also proved to be an effective method for creating steeper slopes.
The rainbow technique was also ideal for beach and foreshore replenishment, although some adjustments were required because vessels sometimes need to work in areas with strong currents. To deal with such situations, the nozzle was shifted from the bow to the side of the vessel. This allows the vessel to direct their bow in the current and steady its position.
As the technique improved, knowledge about the correct mixture of sand and water grew, and the vessel pumps increased in power, the rainbow technique evolved to where it is today: a precise method that can be used to fill land reclamation sites, create islands in the middle of the ocean, and deposit sand at exact locations for beach replenishment projects or foreshore reclamation.
Dubai’s landmark Palm Jumeirah or the archipelago The World could probably only be constructed economically using the rainbow method, introduced for the first time in the 1980s. Before then, trailing suction hopper dredgers discharged their load either by depositing it through their bottom doors or pumping it to shore through a pipeline.
Reclaiming land quicker and at lower costs
Rainbow method
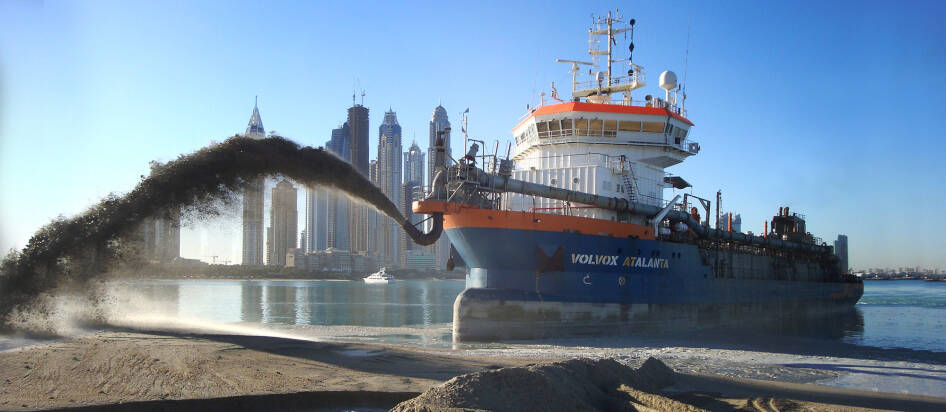
Koos van Oord
Area Manager for Van Oord Offshore
The addition of the Bravenes to our fleet allows us to maintain our leading position in the market. Compared with other subsea rock installation vessels, the Bravenes can install rock very close to offshore platforms such as monopiles in offshore wind parks.
How it started
In the 1950s, we developed the side stone dumping vessel, replacing the manual installation method that had been used for centuries. These vessels were used successfully in shallow waters. It was the first step in improving safety, accuracy and efficiency.
Oil and gas exploration explored deeper waters and new rock installation techniques had to be developed. Once again, Van Oord rose to the challenge and developed its unique flexible fallpipe concept. The first flexible fallpipe vessel ever, the Trollnes, began operating under the Van Oord flag in 1991. Dynamic positioning and a remote-operated-vehicle ensures very accurate placement of rock in deep water. The flexibility of the fallpipe means it can operate in high waves and strong currents. Further investments of the system led to the capability to protecting a pipeline at a record-breaking depth of 1,277 metres by the Stornes, starting a new area of subsea rock installation.
Brave new world
Offshore wind is a growing market for subsea rock installation. Generally, offshore wind parks are located in relatively shallow waters, where waves and currents have a bigger influence on the seabed than in deeper water. That means that larger rocks are needed to guarantee stable protection of foundations placed on the seabed.
The Bravenes has been designed to load both larger and smaller rocks and has the unique ability to install rock in different ways. Equipped with the latest innovations to improve vessel safety and efficiency, such as a fully automatic fallpipe loading and transport system, it raises the bar for the industry.
Subsea Rock Installation (SRI) has been a core element of our business throughout the 150 years of our existence. After the Second World War, Van Oord was already the market leader in this field. At that time, rock was installed by hand. Thanks to a string of in-house and external innovations, manual labour has been replaced by a fully automated system.
Improving safety and efficiency
Subsea Rock Installation
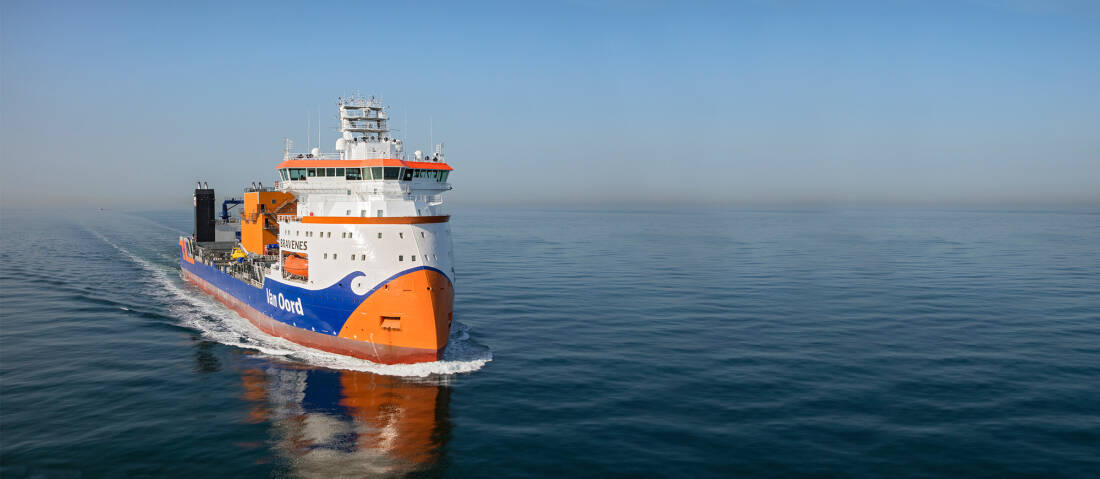
Marcel Krijnen
Deputy Director of the Willem
Barentsz Maritime Institute
As a maritime institute we want to meet the demand for highly qualified personnel in the maritime sector. With the use of our simulators, we can reach that goal. On-the-job experience is always best, but the simulators these days are a really close second and invaluable in our curriculum.
How it started
In the 1970s, dredging professionals wanted to gain more insight into the interaction between equipment and soil. That was the starting point of using simulators to obtain more knowledge. Van Oord played a major role in the implementation of these unique simulators and values their use up to this day.
The world’s first cutter suction dredger simulator came to life in the 1980s and one of Van Oord’s predecessors was involved in developing it. It was also the first time dredging schools started to use this technique to teach new dredging professionals the skills of the trade. The first trailing suction hopper dredger simulator was introduced in 1990s. Both types of simulators changed the manner of training forever.
Ready for all conditions
The simulators have evolved over the years and we currently have three of them in-house giving a realistic view of project situations for three types of equipment. What makes our training programme stand out is that we emphasise on dredging production and automation and that our simulators can simulate any circumstance, from soil type to weather conditions.
We continue to improve and develop our simulators and training programmes and have partnered with the Willem Barentsz Maritime Institute to share best practices. That way, we’ll both be ready to train the dredging professionals of the future.
At Van Oord we know the importance of keeping our professionals’ knowledge and skills up-to-date, and we’re always looking for ways to improve training facilities. The high-tech simulator training center at our Rotterdam head office is the perfect example.
Changing the way we learn
Simulator
Training Center
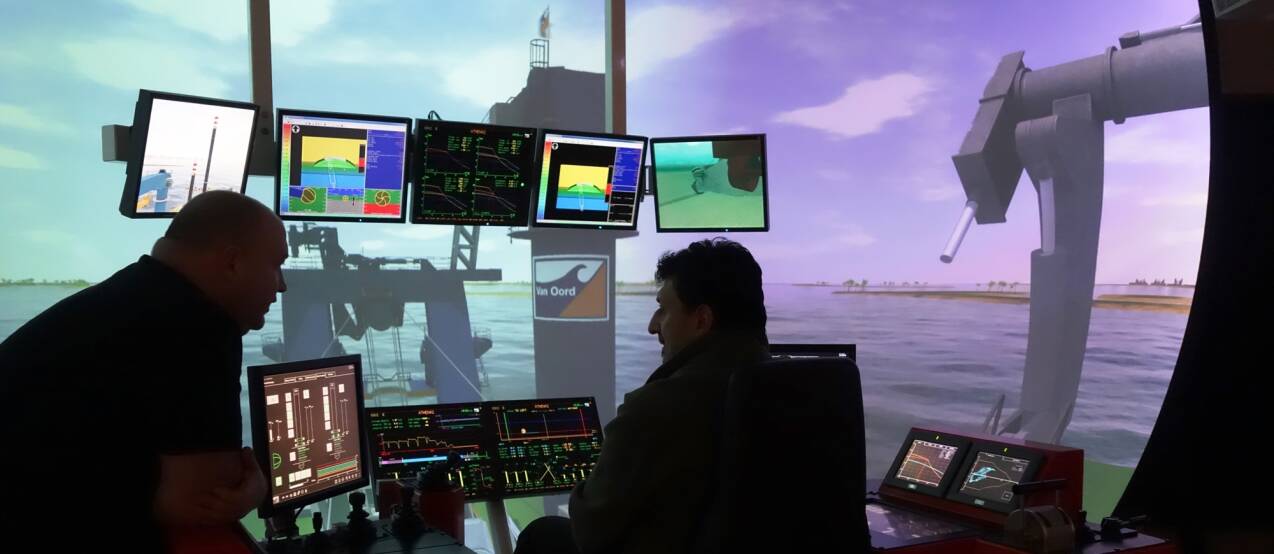